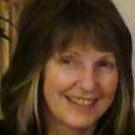
By Gaby Grammeno Contributor
The worker was injured in an incident on 29 April 2022, when he was helping a co-worker move concrete blocks using a front-end loader with a bucket attachment and a lifting chain attached.
It appeared that the bucket – which did not have an approved lifting point – could have blocked the line of sight between the worker operating the mobile plant and the worker attaching the clutch to the concrete block. His fingers were pinched in the chain, resulting in a crush injury that led to the amputation of the tips of his right middle and index fingers.
SafeWork SA issued an enforcement notice prohibiting the activity of loaders lifting or suspending any loads using an unapproved lifting point or device, and a further notice for not providing the worker with the information, training and instruction required to perform the task safely.
After conducting its investigation, SafeWork SA alleged that in failing to provide and maintain a safe system of work and failing to ensure measures were in place to eliminate or minimise the identified risk, the company had committed a Category 2 offence under the Work Health and Safety Act 2012 (SA).
The company responded by offering the regulator an enforceable undertaking – a legally binding commitment to implement a set of work health and safety initiatives designed to deliver tangible benefits for workers, industry, and the community as a whole, as well as resolving the issue that led to the injury and ensuring it would not happen again.
Rectifications already made since the incident
Many workplace changes were made with the aim of preventing any recurrence of such incidents in future.
After initially hiring a forklift with an approved lifting frame, the company replaced it with a new wheel loader with a suitable jib lifting attachment. A review of the company’s eight concrete sites was carried out and the fitness for purpose was assessed for all lifting equipment
Management was restructured to increase depth of oversight, and new roles created with ‘significant capacity to focus on health and safety’.
Training in ‘Life Saving Rules’ was given to all employees and included in induction processes. Senior management were given a due diligence briefing by a legal provider and middle and frontline managers were briefed about WHS duties and related matters.
Safety, health and environment communication boards were installed at all sites to convey information to visitors as well as workers, to ensure a consistent approach.
All up, the company spent almost $430,000 on rectifications.
Changing the workplace culture
The company considered that the incident highlighted problems with its previous risk assessment process, which was a result of a ‘get-the-job-done’ mentality. This attitude was seen to have contributed to the likelihood that potential safety risks would be overlooked, which was made clear in the undertaking.
‘The initiatives set out in this undertaking go beyond the circumstances of the incident itself and seek to embed a “safety-before-anything-else” mindset.’
Proposed action program
In the undertaking, the company proposed to develop and deliver a management training program on ‘Leading a Healthy and Safe Culture’, engage a motivational speaker to address 200 staff, review and improve its risk management standard and processes to spot and fix deficiencies, run risk management awareness sessions, develop updated resources for staff and a new, business-wide health and safety logo for vehicles and hi-vis workwear.
A key feature of the proposed actions is the construction of a $100,000 fitness, health and wellbeing hub at one of its facilities. The Hub will include a gym, a health professional consulting room where staff can access programs including mental health, general health assessments, skin checks, programs for improving grip strength, quitting smoking, blood donations and exercise advice, as well as other facilities.
The business will also prepare and deliver a presentation about the incident and lessons learnt to the Cement, Concrete and Aggregates Association, stage a mock trial based on a scenario similar to the incident, and work with a provider of training for former prisoners to help them obtain construction certification.
A $5,000 donation will be made to each of five Men’s Sheds to fund health and safety-related training or equipment, a ‘Hand Safety Awareness’ training package will be developed and shared with the Men’s Sheds and the company will extend its Tier 1 support for Mates in Construction.
The employer undertook to widely disseminate information about the undertaking and its commitments to all relevant parties, and to ensure its WHS management system is audited by third party auditors.
The company estimated that the minimum spend for the proposed actions will be around $462,000.
As part of the undertaking, the company granted SafeWork SA a permanent, irrevocable, royalty-free, world-wide, non-exclusive licence to use, publish, publicise, adapt or modify any materials developed as a result of the undertaking. The intention is to encourage other enterprises engaging in the same types of work activities to benefit from the company’s response to the accident.
The regulator accepted the company’s undertaking in lieu of prosecution, taking the view that the undertaking is the preferred enforcement option because it prompts organisational change which goes beyond the company involved. SafeWork SA will monitor compliance with the commitments set out in the undertaking.
What it means for employers
The concrete company considers the undertaking an opportunity to make a significant investment in improving its systems of work for the benefit of its employees and to help bring about change in the wider industry and community. Heavy lifting jobs present a range of risks, and employers may benefit by improving their own systems of work in the light of the improvements set out in this agreement.
Read the undertaking
Enforceable undertaking: MSP Group T/A Hallett Concrete Pty Ltd